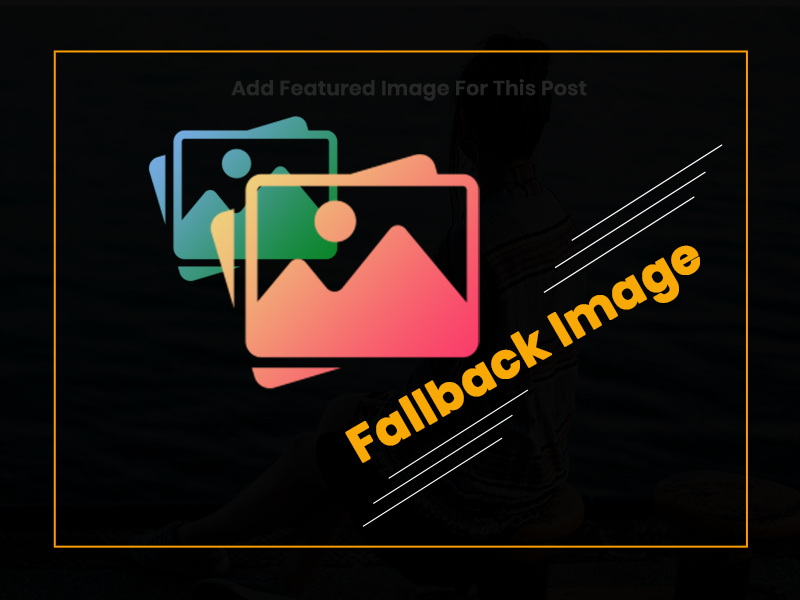
Concealing The Crack – Maintenance Approaches Extending Equipment Life
No manufacturing operation would ever be capable of existing or being successful in the slightest without the help of their machinery. Properly running machinery is only made possible through the help of maintenance scheduling fitting their needs. This is why it’s imperative for businesses to develop a maintenance strategy that fits the needs of their equipment accordingly. Understanding that each and every piece of equipment will likely need their own unique care, it’s clear that finding the right strategy is going to be difficult. This post will detail two of the most popular maintenance approaches, preventive and predictive maintenance, and how the strategies can blend for the needs of different equipment.
Preventive maintenance has been the standard for manufacturing organizations for some time. This strategy is rather simple: maintenance all pieces of equipment at set time intervals. For most organizations, this depends on the current statuses of their different pieces of equipment and the age of these pieces of equipment.
Predictive maintenance, on the other hand, is a much more dynamic approach that manufacturing organizations have been taking in recent years. This strategy uses real time data collected from a fleet’s equipment to determine the most optimal maintenance schedule. Unlike preventive maintenance, this would mean that certain pieces of equipment wouldn’t need such regular maintenance compared to the rest of a fleet. Maintaining this equipment as needed is much more effective, but the downside of these systems are the exuberant costs associated with their implementation.
Even with such insurmountable costs, the implementation of these systems continues to become easier. The organizations that can afford these systems are leading the way in that effort. These systems are connected to the Internet of Things, meaning as more and more machines become compatible and are added onto this network, the more accurate the information derived from the equipment can be. With more accurate reporting, comes more accurate insight into what is causing a piece of equipment troubles. Identifying this trouble makes mitigating the risk of failure much more likely for these organizations. Which can lead to decreased down-time for any piece of equipment.
Regardless of these advantages, more often than not these systems will remain out of reach for a majority of organizations. Their inaccessibility might not be too much of an issue, though. These systems bear a very high cost to begin, but they also require near seamless integration in order to get the most out of them. Another downside is the required retraining of existing employees to work alongside these new systems and new platforms that may be required as a result of these systems. However, if your business has enough capital to support the transition, the benefits will likely outweigh the cost. It may just take a slight adjustment period.
Every business is interested in identifying the ways that their maintenance can contribute to long term success. There is no way to achieve this level of success without the right maintenance approach for each piece of equipment. To learn more about these maintenance strategies and philosophies, take a minute to read on to the infographic highlighted on this post. Courtesy of Industrial Service Solutions.